Author: Editorial board
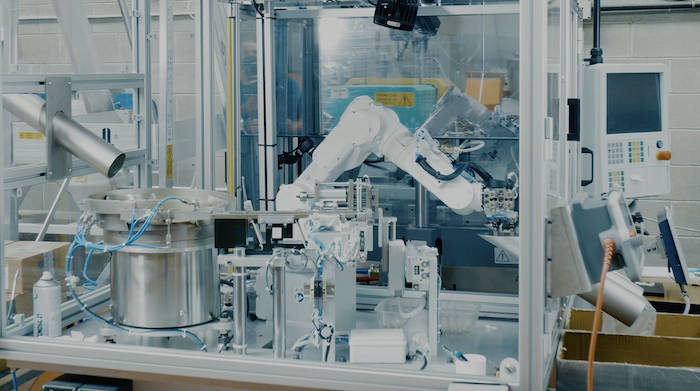
Manufacturing Execution System: optimising production cycles
The introduction of the new automated co-moulding production workstation in the SLIM production plant required the implementation of the Manufacturing Execution System (MES). This term refers to a computerised system that aims to manage and control the company's entire production process in an integrated and efficient manner.
For SLIM, this is a step towards the so-called Industry 4.0, which is based on the use of a combination of technologies designed to promote automated, planned and interconnected production. It is a renewal of processes and systems, aimed at improving the level of service offered to our customers across the board. Let's find out why.
Technology and innovation guide us on a daily basis, from production processes to the design of customised lighting solutions. Discover the innovative lighting solutions developed in collaboration with major companies. Click on the button below and download the free document on SLIM's success stories!
Reduction of the cycle time: the benefits
The Manufacturing Execution System detects and uses real-time data to optimise the various activities related to the moulding department and the production cycle. This accurate data makes it possible to distribute precise information to the various production machines and monitor activities in real-time, thus facilitating daily operations. The primary benefit is reduced cycle time. Thanks to the rapid reaction of the interconnected machinery and a greater focus on reducing non-value-added activities, processes are carried out efficiently and with considerable time savings. The resulting benefits include production optimisation and a reduction in the cycle time per faston mount.
Production optimisation
In parallel with the installation of the automated co-moulding workstation, the existing presses in our plant were brought online with the implementation of the MES. These seven machines, after being interfaced via electronic boards and specific protocols, are now able to transmit a series of data to the computerised system. The software makes it possible to control the progress of the production phases, the management of production resources, the status of each machine and the traceability of the product. The MES engineer has an overview of all the activities carried out and to be carried out. This enables him to make considerations in terms of organising moulding orders and the production of minimum and multiple batches, with a view to optimising production not only on a daily and weekly basis but over the long term.
Cycle time reduction for faston mount production
Another benefit of automated and interconnected production is the reduction in cycle time for the production of the 6.3x0.8 mm faston mount component. The skilful management of the software by the operator, who determines the succession of moulding orders by activating the specific programmes required according to plastic material and colour, means that machine downtime is reduced, bringing the process to maximum efficiency. Currently, the cycle time has been reduced by 15% in terms of seconds. There has also been an increase in daily production of more than 30% due to the machine's consistent operation.
Department load planning
MES helps in management, to be more attentive not only to processes but also to costs.
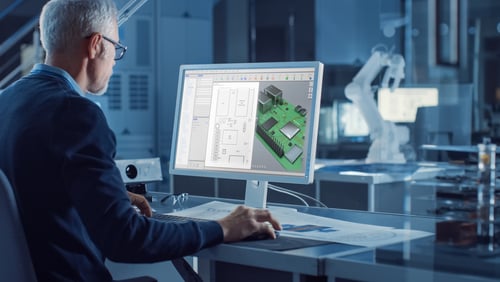
Computerised control and management of the department
The continuous exchange of information, between the press and the system, from the launch of the order to the finished product, provides a series of data to our operators, who in the long run will be able to have a data history. This will enable them to understand how to further improve the entire production chain. Computerised control and management of the stamping and production department, therefore, helps in the overview of the period, the orders to be produced and to recalculate the times from scratch if there is a change.
Are you looking for an efficient and timely supplier? Feel free to contact us, we will be able to provide you with the right solution precisely and quickly.